Meet our LRVS 2024 Speakers!
Here's a quick look at some of our Speakers and Panelists for LRVS 2024 along with the topics they will be discussing.
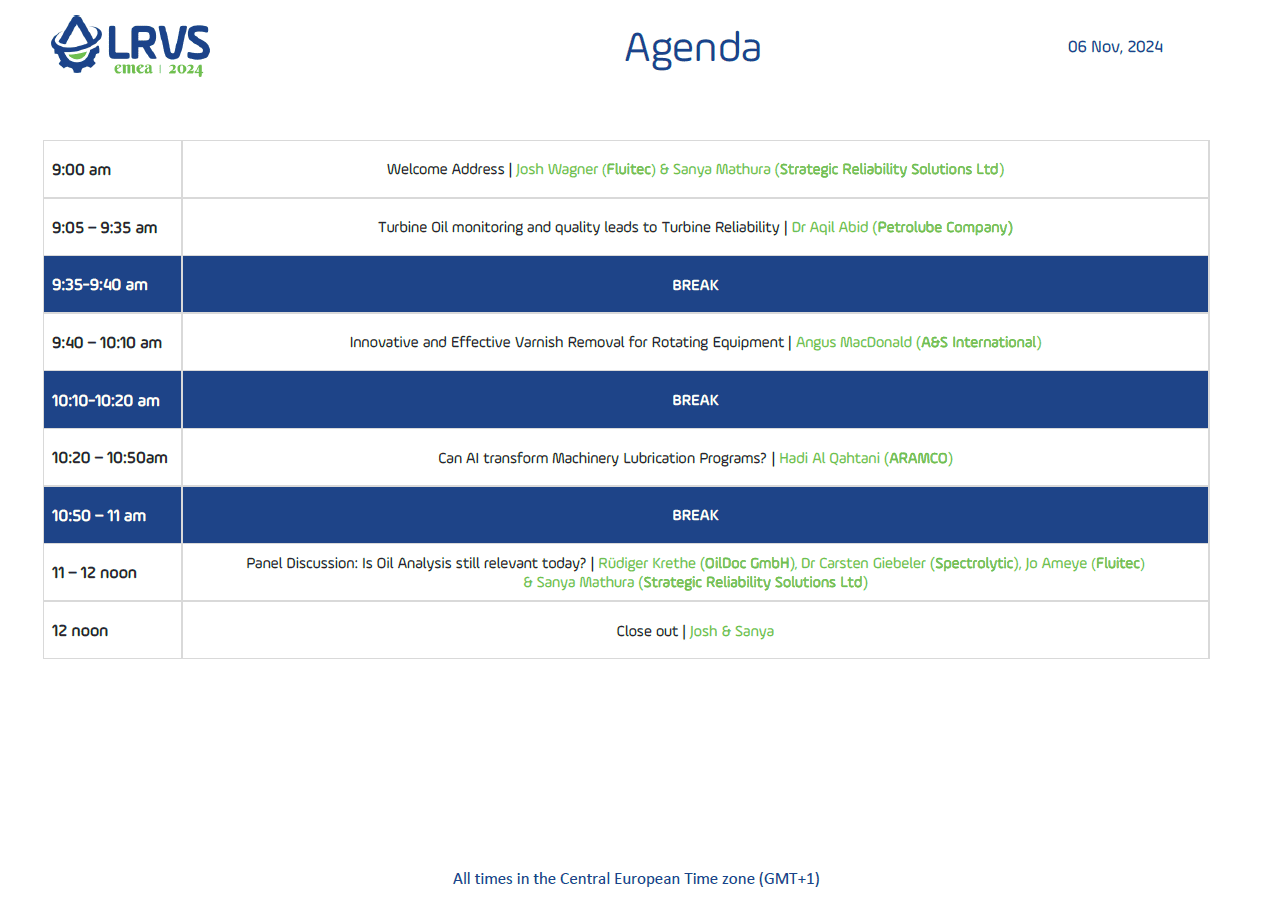
LRVS 2024 EMEA Speakers
Dr Mohammad Aqil Abid
Dr Mohammad Aqil Abid
Technical Service Specialist at Petrolube
Turbine Oil Monitoring and Quality leads to Turbine Reliability
Turbine Oil Monitoring and Quality leads to Turbine Reliability
Turbine Oil Monitoring and Quality leads to Turbine Reliability
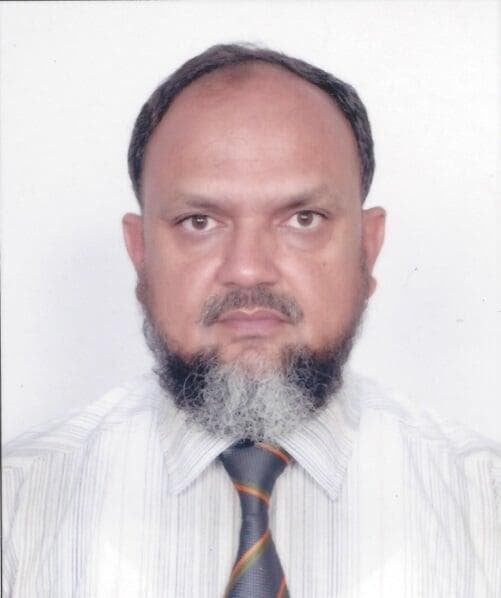
This Presentation examines the monitoring and analyzing of a turbine's condition through a systematic way, which can help identify turbine problems before they result in a major failure. It also outlines a few basic steps in Turbine and Turbine Oil and the importance of its Monitoring through Root Cause analysis (RCA) which may be affected due to contamination. Such contamination can result in increased maintenance requirements or premature component failure. Its Corrective and Preventive action (CA and PA) as well as Hydraulic valve failure analysis will also be discussed.
Angus MacDonald
Angus MacDonald
Director at A&S International
Innovative and Effective Varnish Removal for Rotating Equipment
Innovative and Effective Varnish Removal for Rotating Equipment
Innovative and Effective Varnish Removal for Rotating Equipment
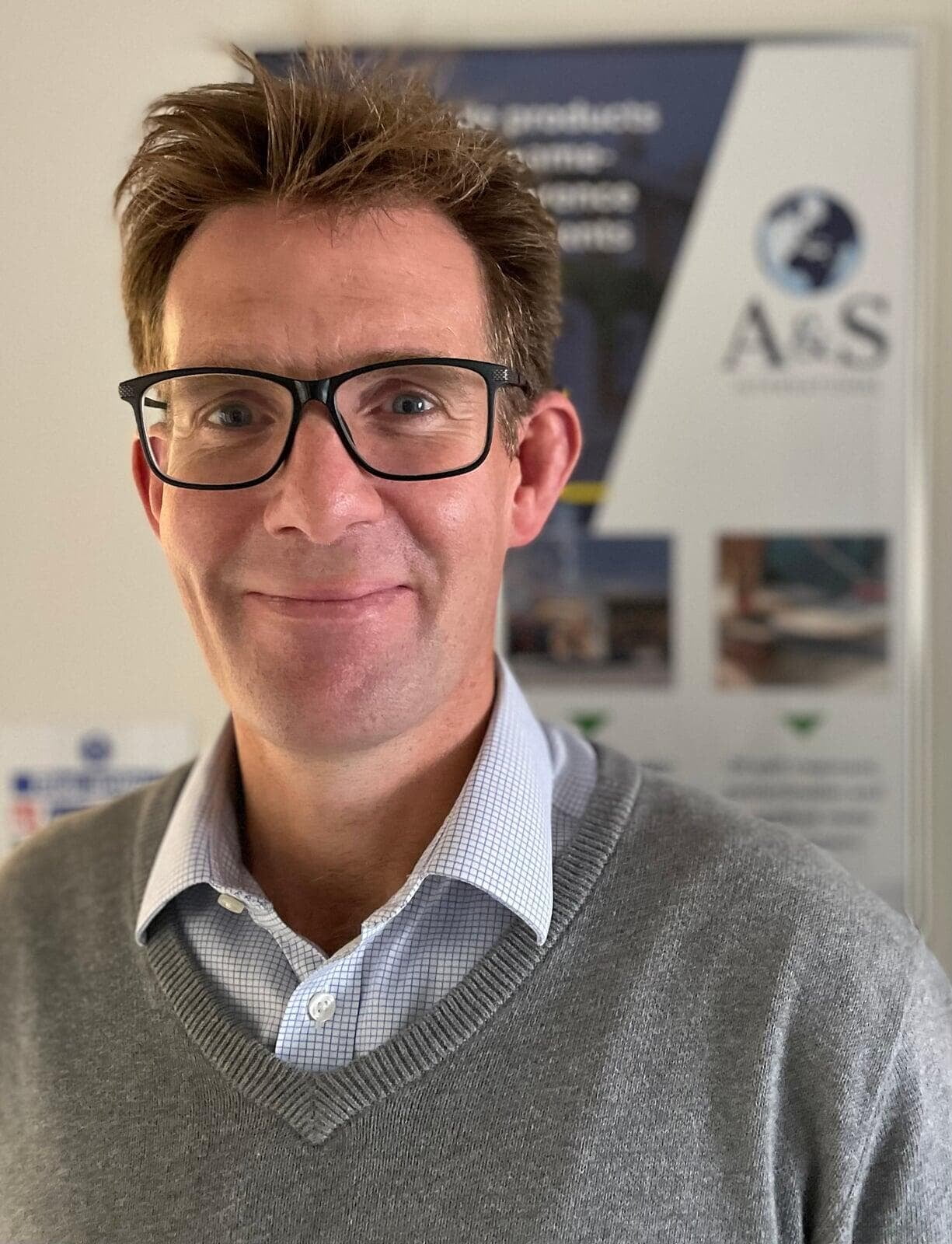
Varnish can take many forms within the industrial sector. One of the best ways to study varnish is to examine some of its appearances in the field. In this session, we will explore a range of case studies in the UK where some innovative and effective varnish removal techniques were used. Some of the industries covered include plastics, plastic injection molding, offshore oil & gas and a variety of applications including turbines & hydraulics.
Hadi Al Qahtani
Hadi Al Qahtani
Senior Engineering Consultant at Saudi Aramco
Can AI transform Machinery Lubrication Programs?
Can AI transform Machinery Lubrication Programs?
Can AI transform Machinery Lubrication Programs?
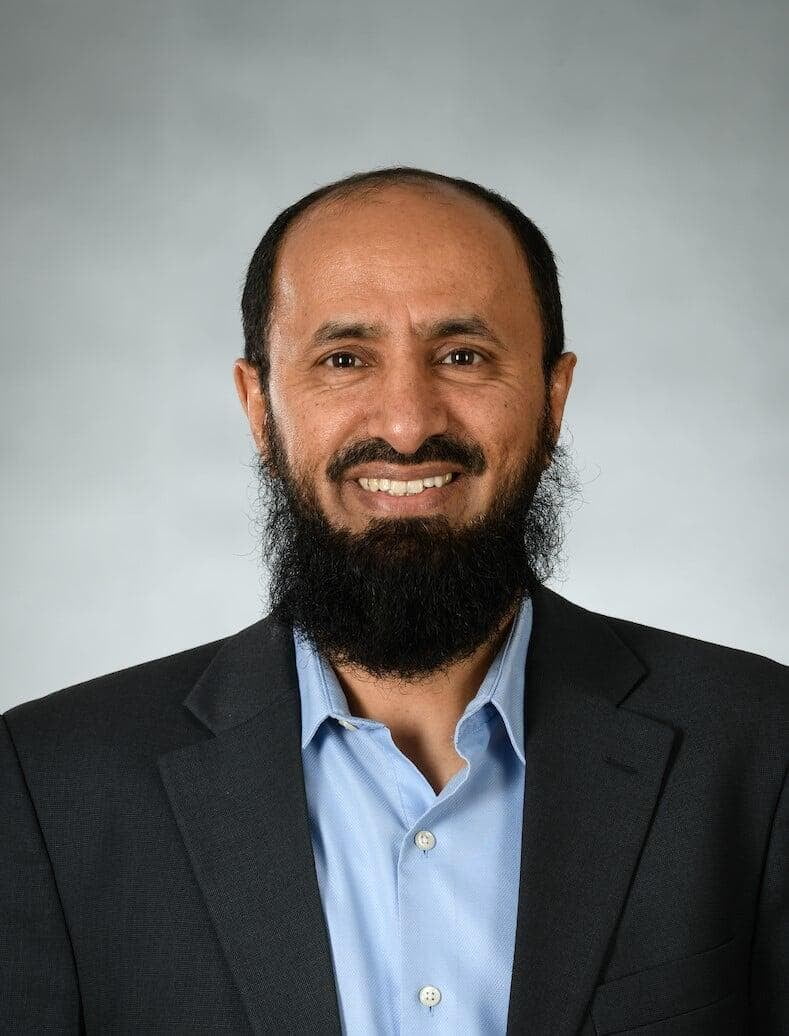
AI in lubrication condition monitoring and prediction is expected to grow in the next few years tremendously for both offline data (sample analysis) and on-line data (sensors). AI can transform the application and management of machinery lubricants by analyzing massive data from machine operations to detect early signs of equipment wear and tear caused by improper lubrication, flagging potential failures before they become critical. AI enables predictive maintenance by identifying when lubricant properties are degrading or when machinery needs service. This proactive approach increases safety, minimizes downtime, and reduces repair costs. In this presentation, successful deployments and realized benefits across industries in addition to several challenges which hinder AI widespread adoption and effectiveness in machineries lubrication will be presented.
Panel Discussion: Is Oil Analysis still relevant today?
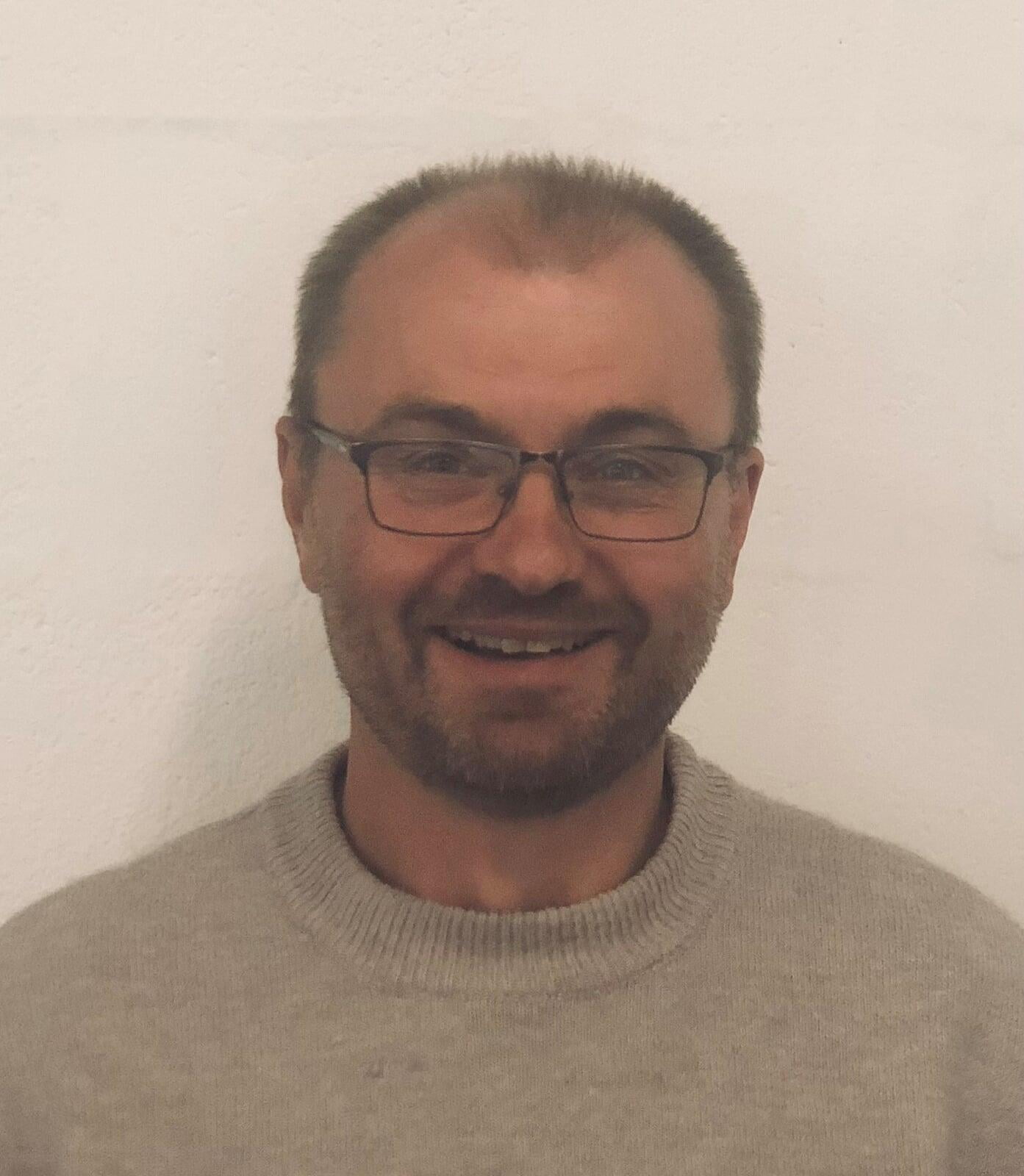
Dr Carsten Giebeler
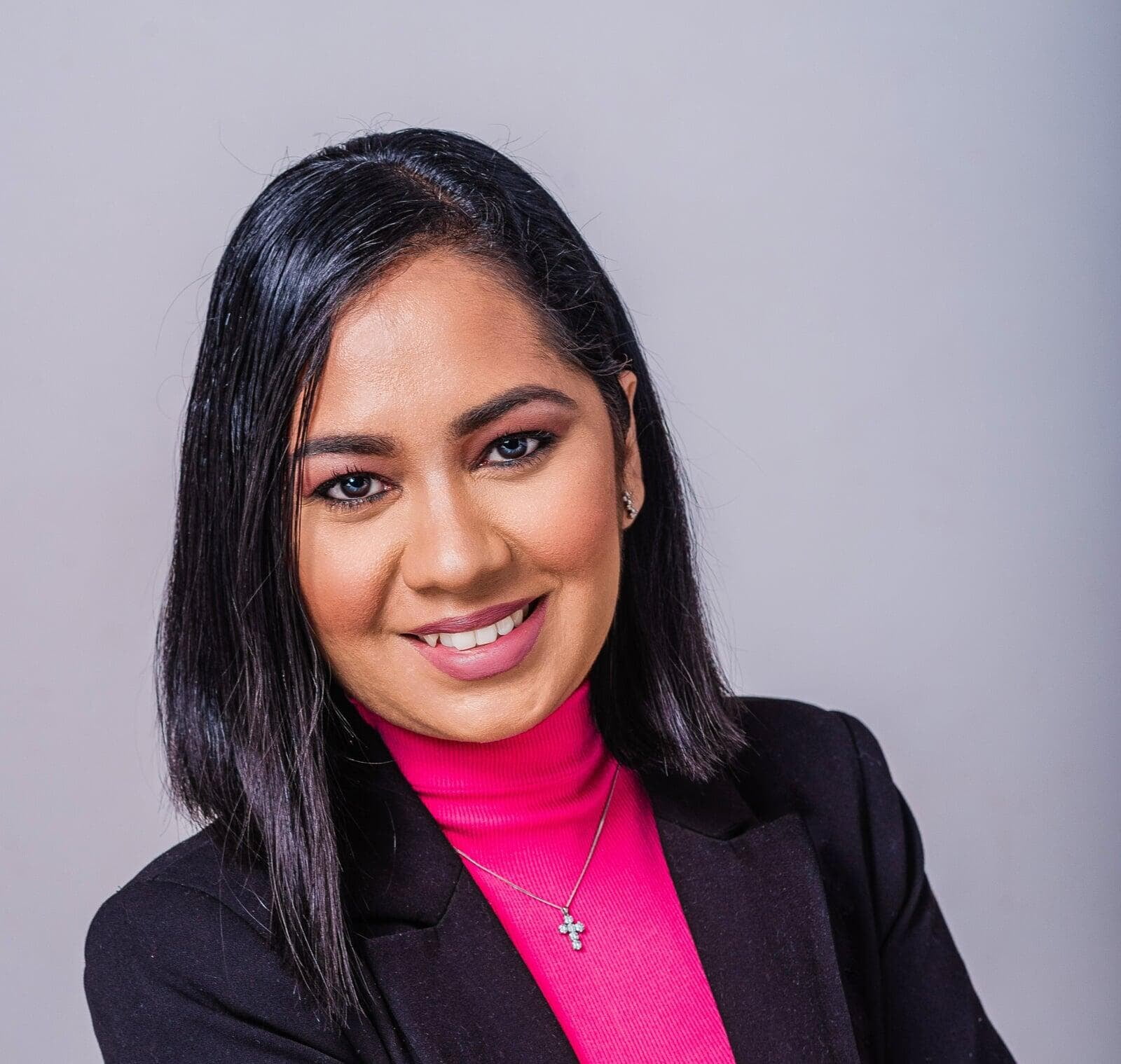
Sanya Mathura
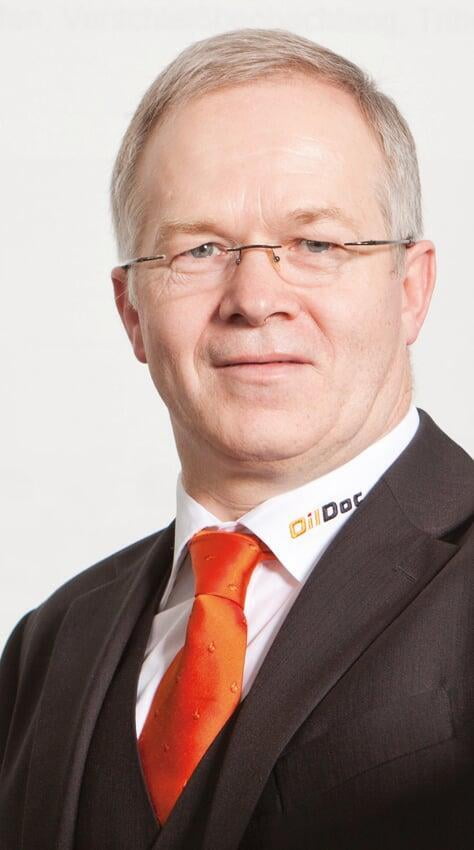
Rüdiger Krethe
Rüdiger Krethe
OilDoc GmbH
Jo Ameye
Jo Ameye
Fluitec
LRVS 2024 APAC Speakers
Rafe Britton
Rafe Britton
Technical Specialist at Lubrication Expert
Non Turbine Varnish
Non Turbine Varnish
Non Turbine Varnish
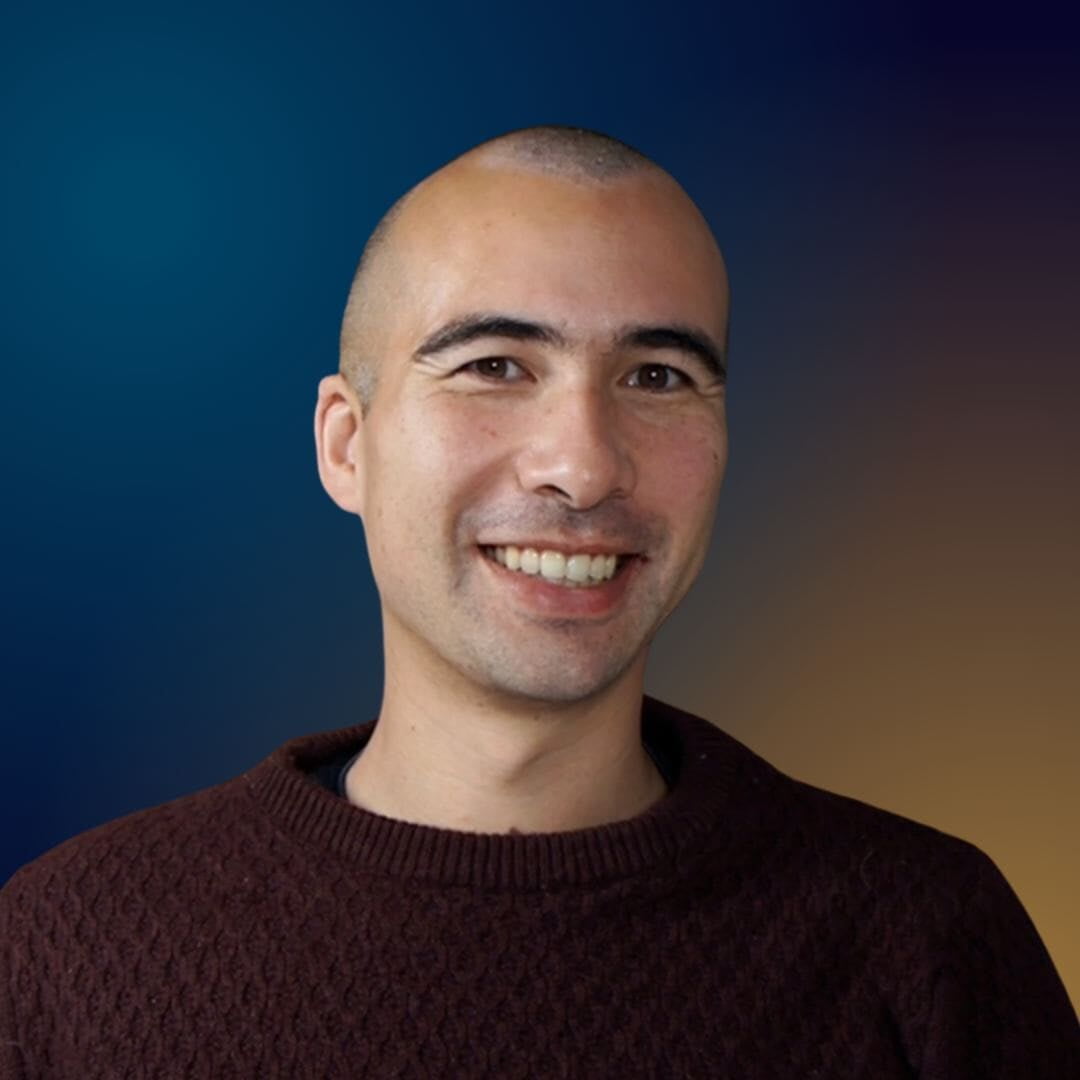
To-date, much of the emphasis in varnish removal has been placed on turbomachinery systems - and rightly so given its prevalence, asset costs and downtime costs. But varnish is a catch-all term for deposit formation in lube oil systems that can also affect gears and hydraulic systems. In this session, we'll look at how that varnish can form, where it is likely to show up, and what we can do to prevent or remove it.
Japan Lube Oil Management Experience 2023
Japan Lube Oil Management Experience 2023
David Lee
David Lee
Principal Fleet Manager,
SOLAR Turbines
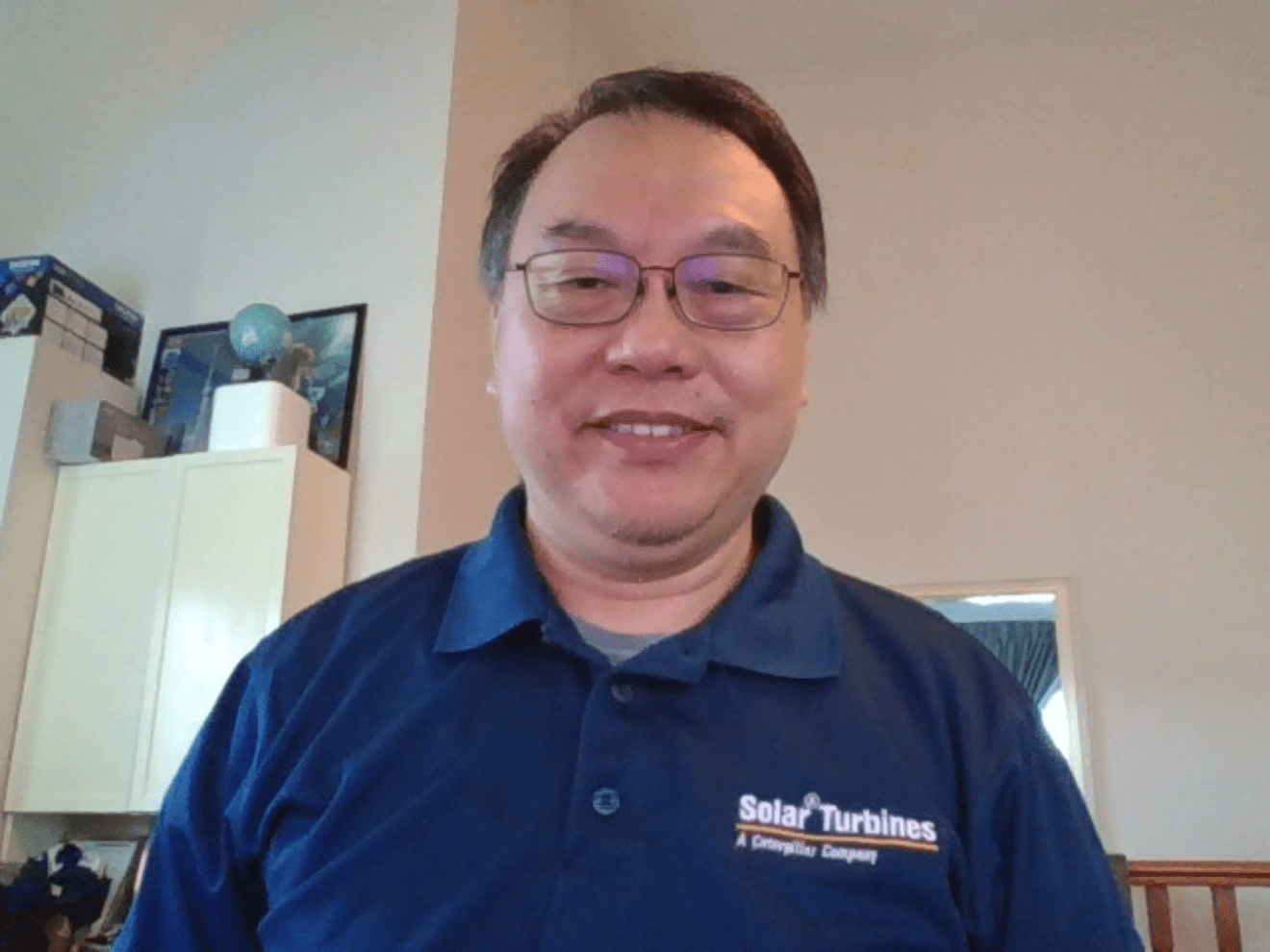
Tomoyuki Kajiura
Tomoyuki Kajiura
Fleet Manager,
SOLAR Turbines
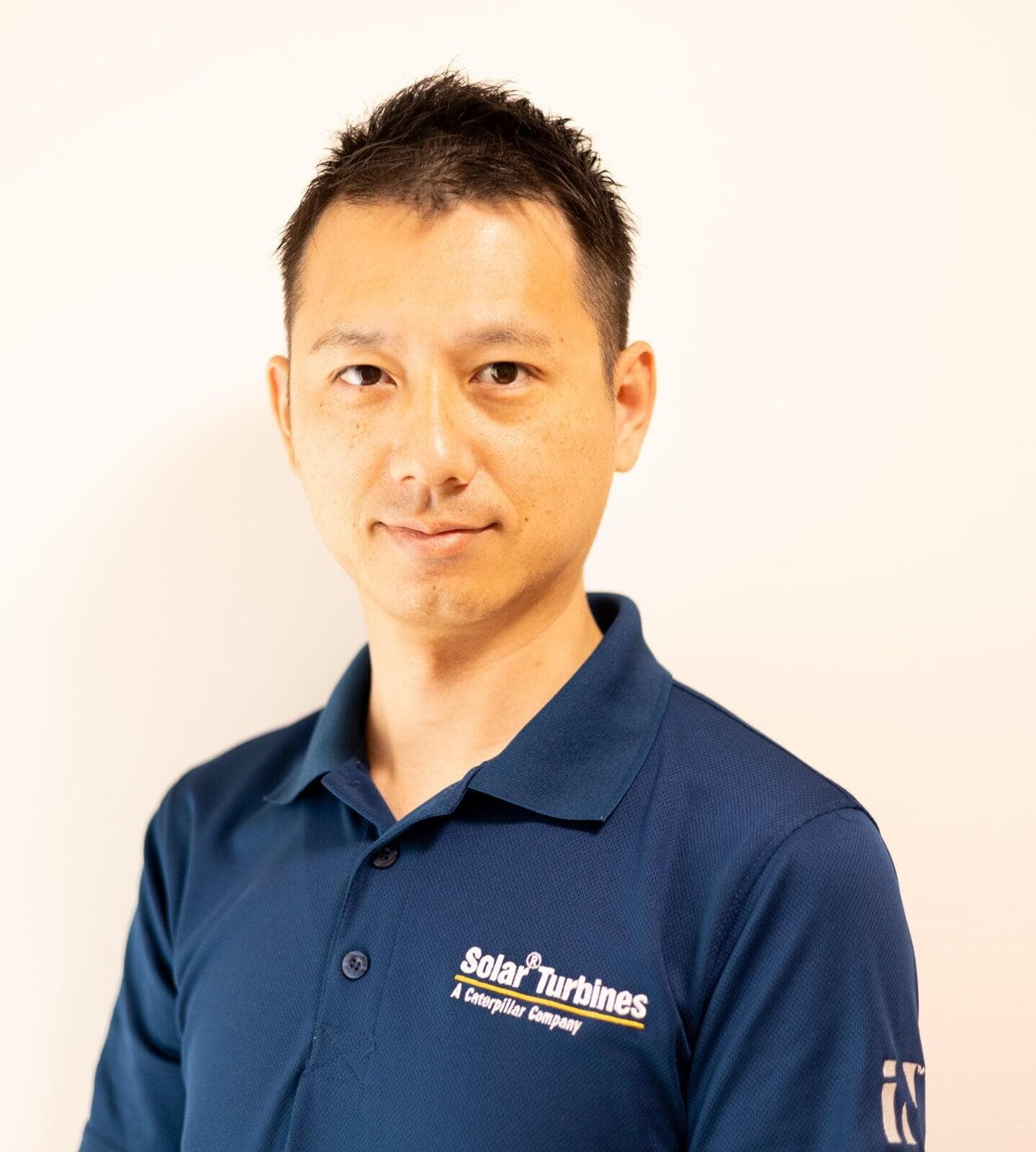
The Japan Fleet of Solar Turbines exhibit many types of learnings for those within the field. In this session, David And Tomo will take the audience through some learnings and experiences that they have encountered while working on these turbines in some harsh environments. They will present key findings on ways to handle particular challenges and solutions they found within their fleet.
Preeti Prasad
Preeti Prasad
Senior Technical Engineer at ECOLAB
Connecting the dots in Maintenance Best Practices
Connecting the dots in Maintenance Best Practices
Connecting the dots in Maintenance Best Practices
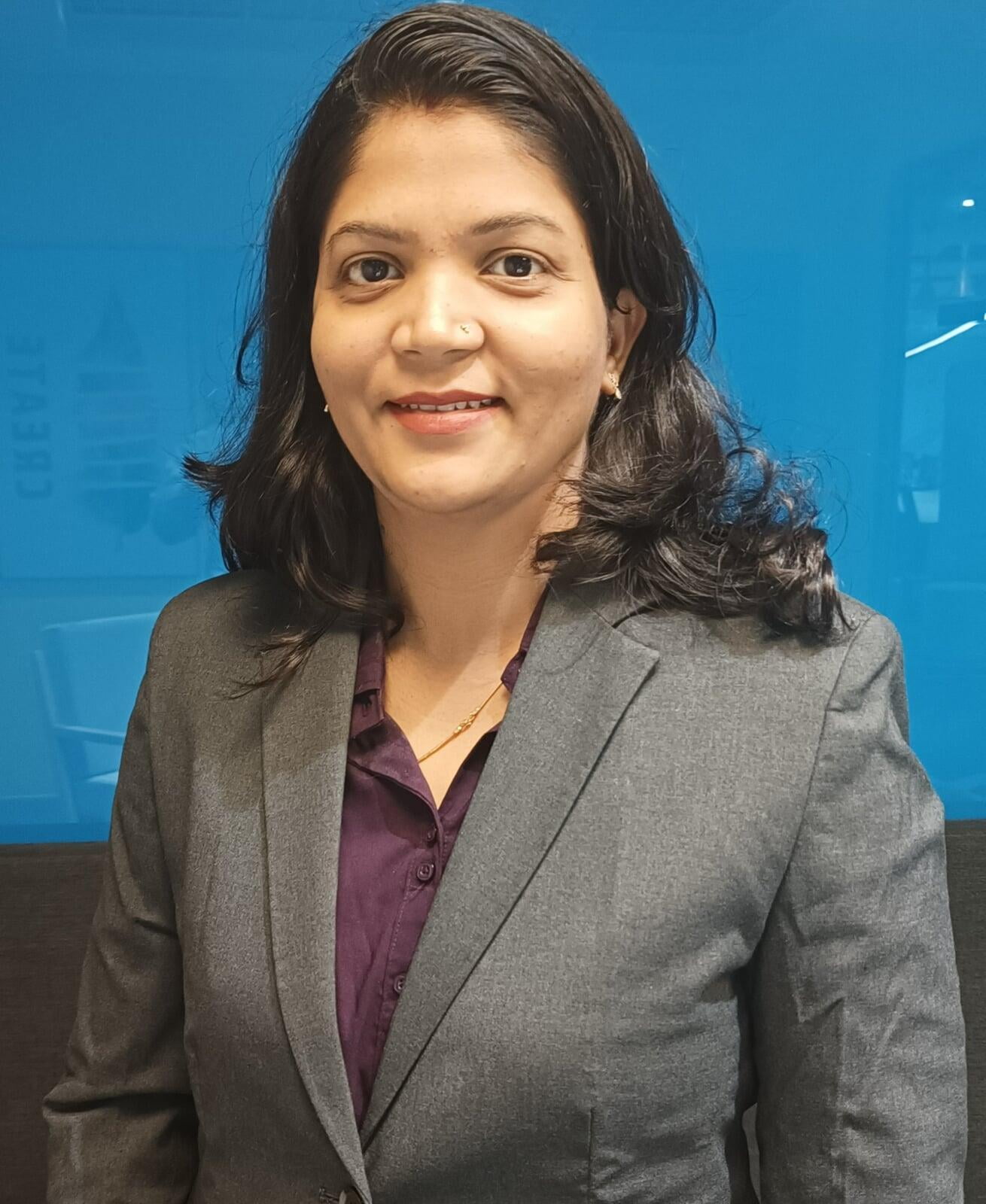
What qualifies a practice as routine or best practice, and how is it evaluated? A strategy, procedure, approach, or methodology is considered a "best practice" if it yields better outcomes with fewer unanticipated troubles. The availability of assets in a desired state is contingent upon implementing best practices in maintenance and reliability. Maintenance
Panel Discussion: New Technologies in the Lubrication Space
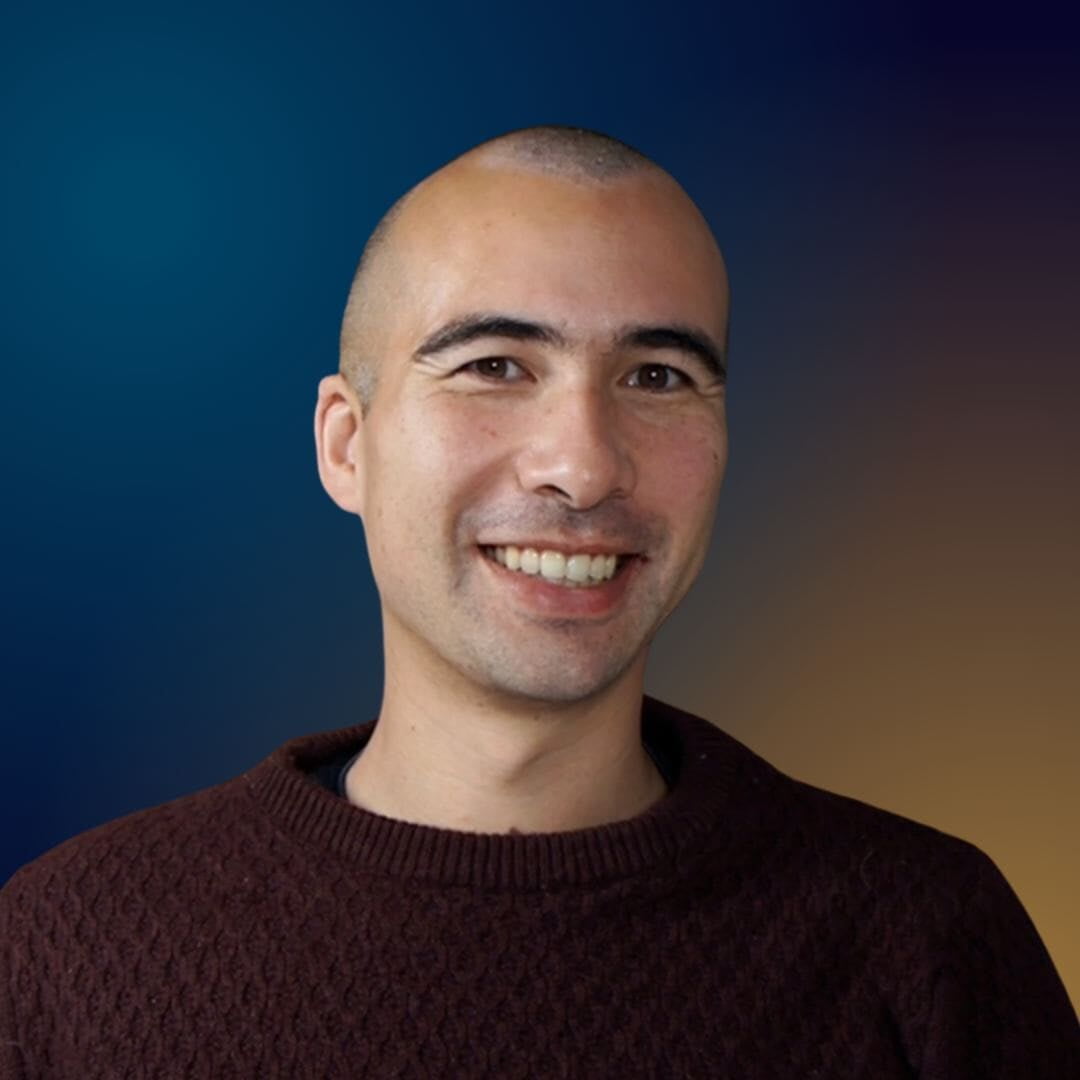
Rafe Britton
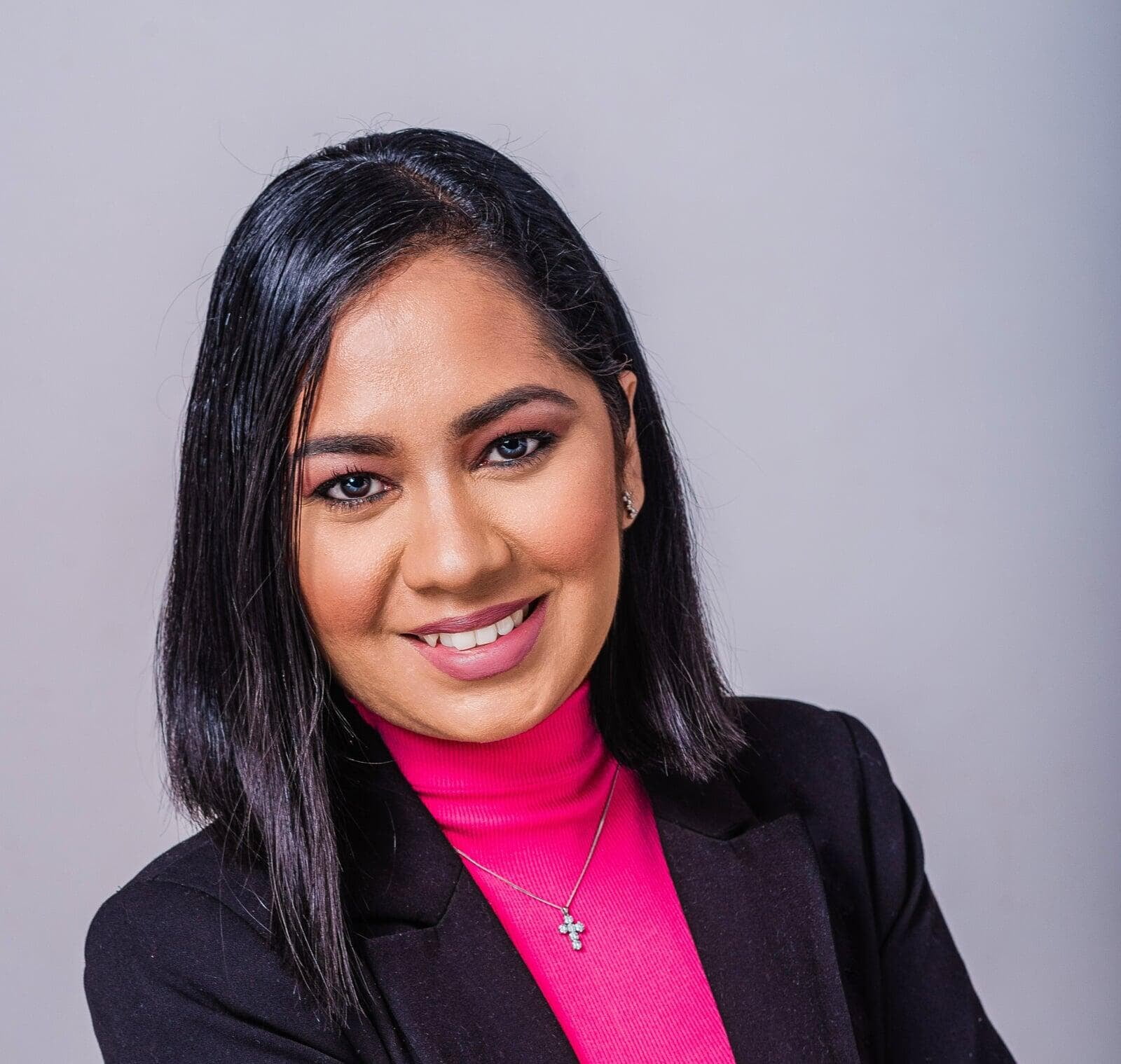
Sanya Mathura
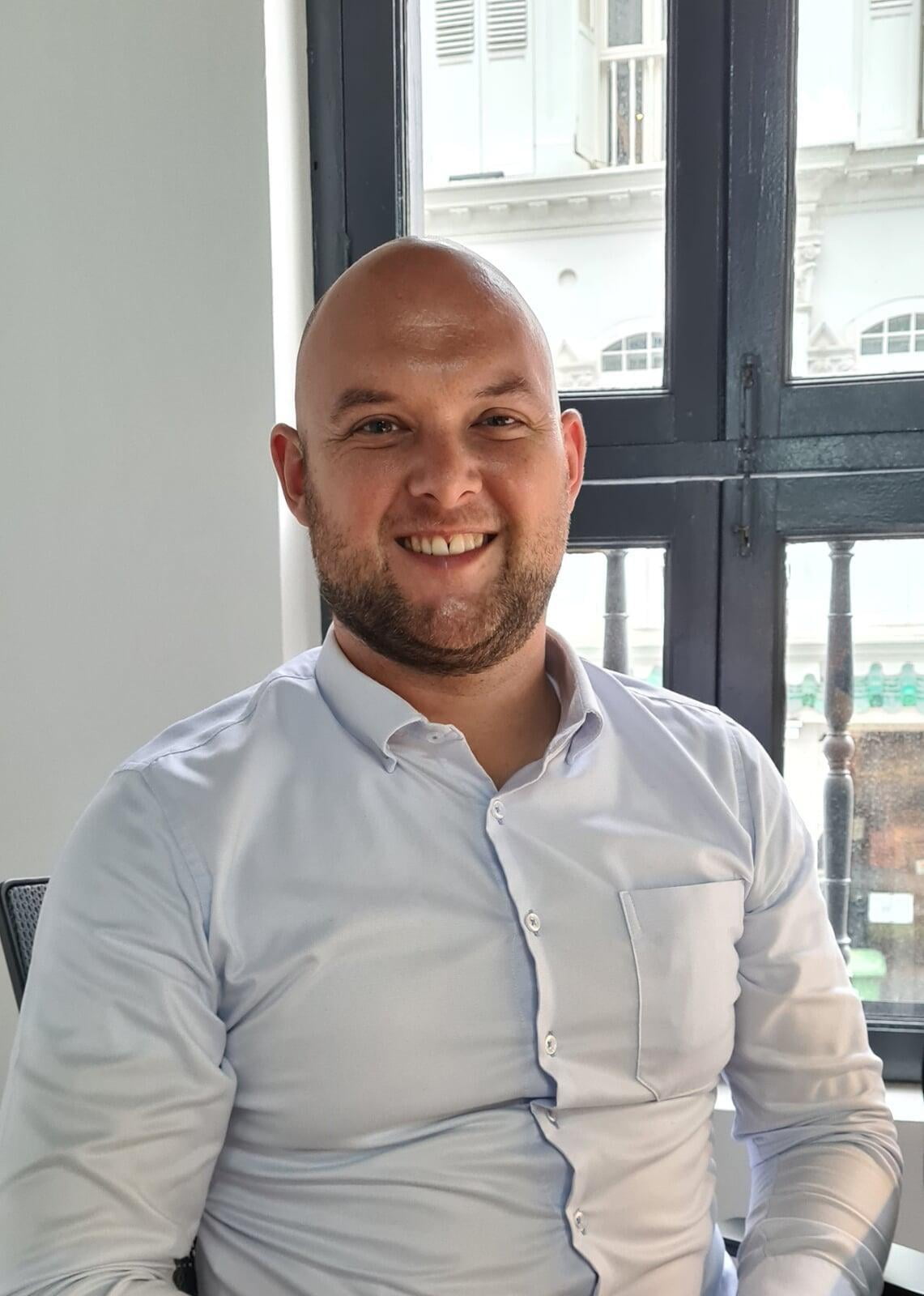
Lars van Dijk
Lars van Dijk
Fluitec
LRVS 2024 AMER Speakers
Building a P-F Curve - A Practical example in Industry
Building a P-F Curve - A Practical example in Industry
Hassan Abdelnabby
Hassan Abdelnabby
Mechanical Maintenance Deputy Director of AL Zeina Tissue Mill Company
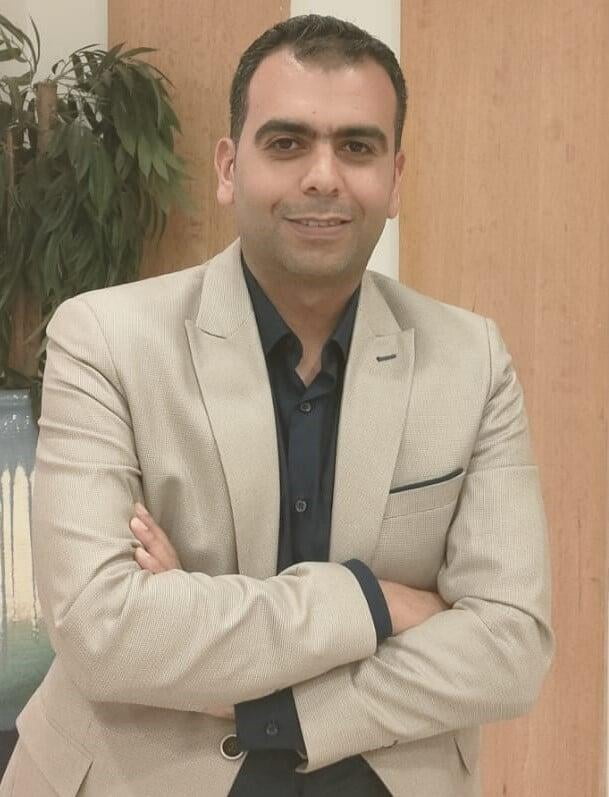
André-Michel Ferrari
André-Michel Ferrari
Owner of Cogito Reliability Inc
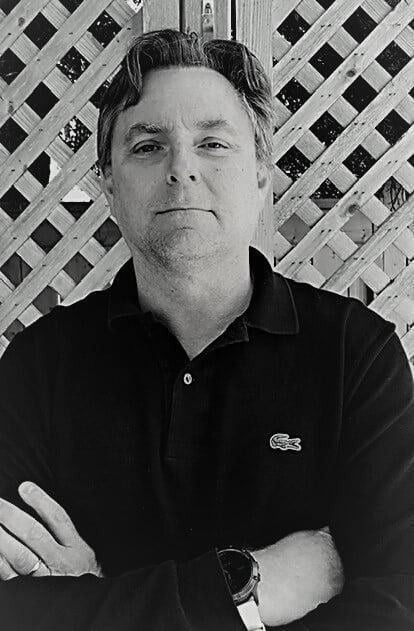
A P-F Curve is used in the Maintenance and Reliability world to combine two concepts: asset degraded condition (still functioning) and failure (loss of function). Its main objective is to guide an operator as to when a repair is due based on the health status of the asset.
In this presentation, the two authors collaborate and use real life data from a manufacturing plant to build a P-F curve. The first part of the presentation covers the construction of the curve using Reliability Engineering principles. The second part applies the learnings from the P-F curve directly into the Asset Management program.
Mike Johnson
Mike Johnson
President of AMRRI
From Cost Center to Competitive Advantage: Creating an Effective Lubrication Plan
From Cost Center to Competitive Advantage: Creating an Effective Lubrication Plan
From Cost Center to Competitive Advantage: Creating an Effective Lubrication Plan
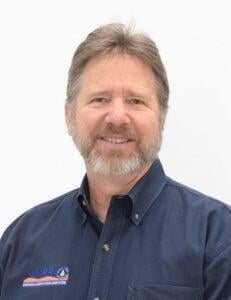
This session offers an in-depth exploration of the strategic development of a precision-driven lubrication regimen to enhance equipment reliability. It addresses the challenge of transitioning routine lubrication from a maintenance task to a core component of competitive advantage.
Creating such a plan is often ambiguous, and engineers may struggle to create a robust and accurate lubrication work plan. Mike Johnson will provide a roadmap to build an efficient and reliable machine lubrication service plan.
The presentation will provide insights into the importance of lubricant selection, application methods, and equipment maintenance schedules. The presenter will also touch on the role of technology in creating a precision lubrication work plan.
Participants will acquire a holistic understanding of creating a strategic lubrication plan that prevents equipment failure and positions lubrication as a key element in achieving operational excellence and competitive differentiation.
Blair Fraser
Blair Fraser
Vice President of UE Systems
From Manual Greasing to Autonomous Lubrication: The Evolution of Bearing Lubrication Technology
From Manual Greasing to Autonomous Lubrication: The Evolution of Bearing Lubrication Technology
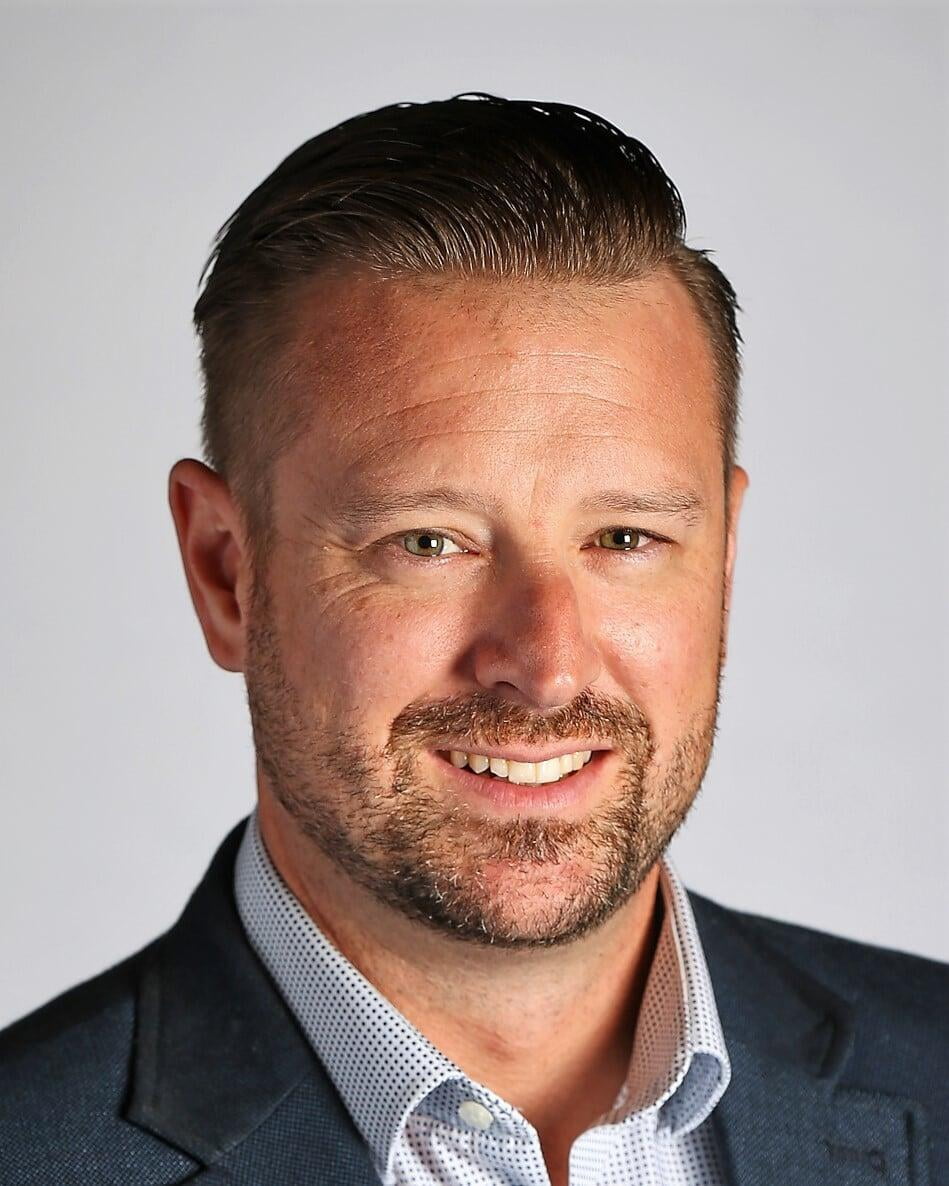
The evolution of bearing lubrication technology has been marked by significant milestones, from the laborious task of manual greasing to the sophisticated era of autonomous lubrication systems. "From Manual Greasing to Autonomous Lubrication: The Evolution of Bearing Lubrication Technology" traces this transformative journey, highlighting the advancements that have redefined maintenance protocols and equipment reliability.
Traditional manual lubrication methods, while foundational, were fraught with the risks of human error, inconsistent application, and inefficiency. The advent of automated lubrication technologies marked a pivotal shift towards precision, consistency, and optimization, culminating in the development of intelligent systems capable of real-time monitoring and response.
These systems, equipped with ultrasound and vibration sensors, not only apply the precise amount of lubricant based on condition monitoring but also gather critical data to inform maintenance decisions, extending the life of machinery and enhancing operational uptime. This presentation explores the trajectory of these innovations, the impact on industrial maintenance, and the future of bearing lubrication as we embrace a fully automated, data-driven approach.
Panel Discussion: Preparing your lube systems for TARs
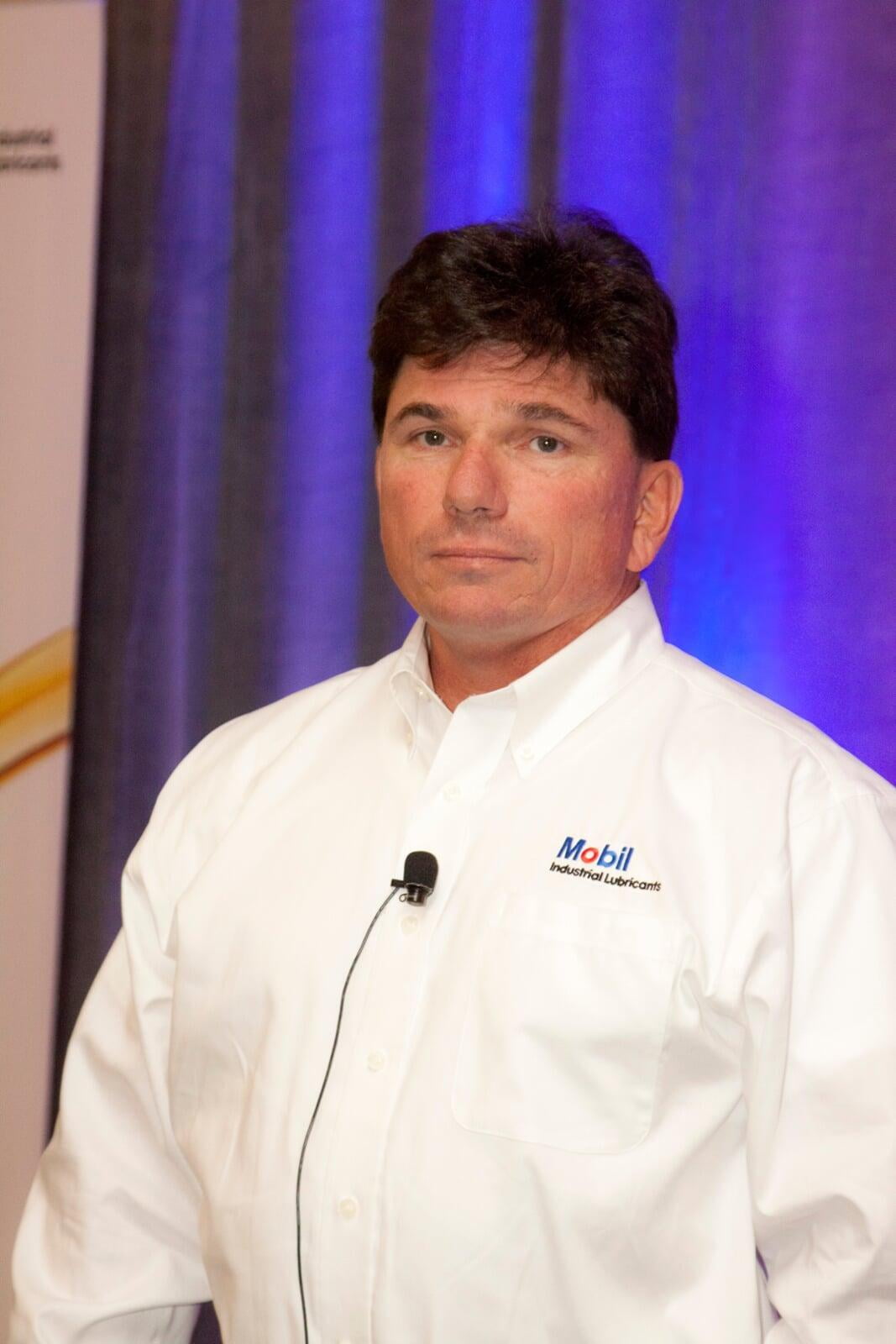
Jim Hannon
Robert Torres
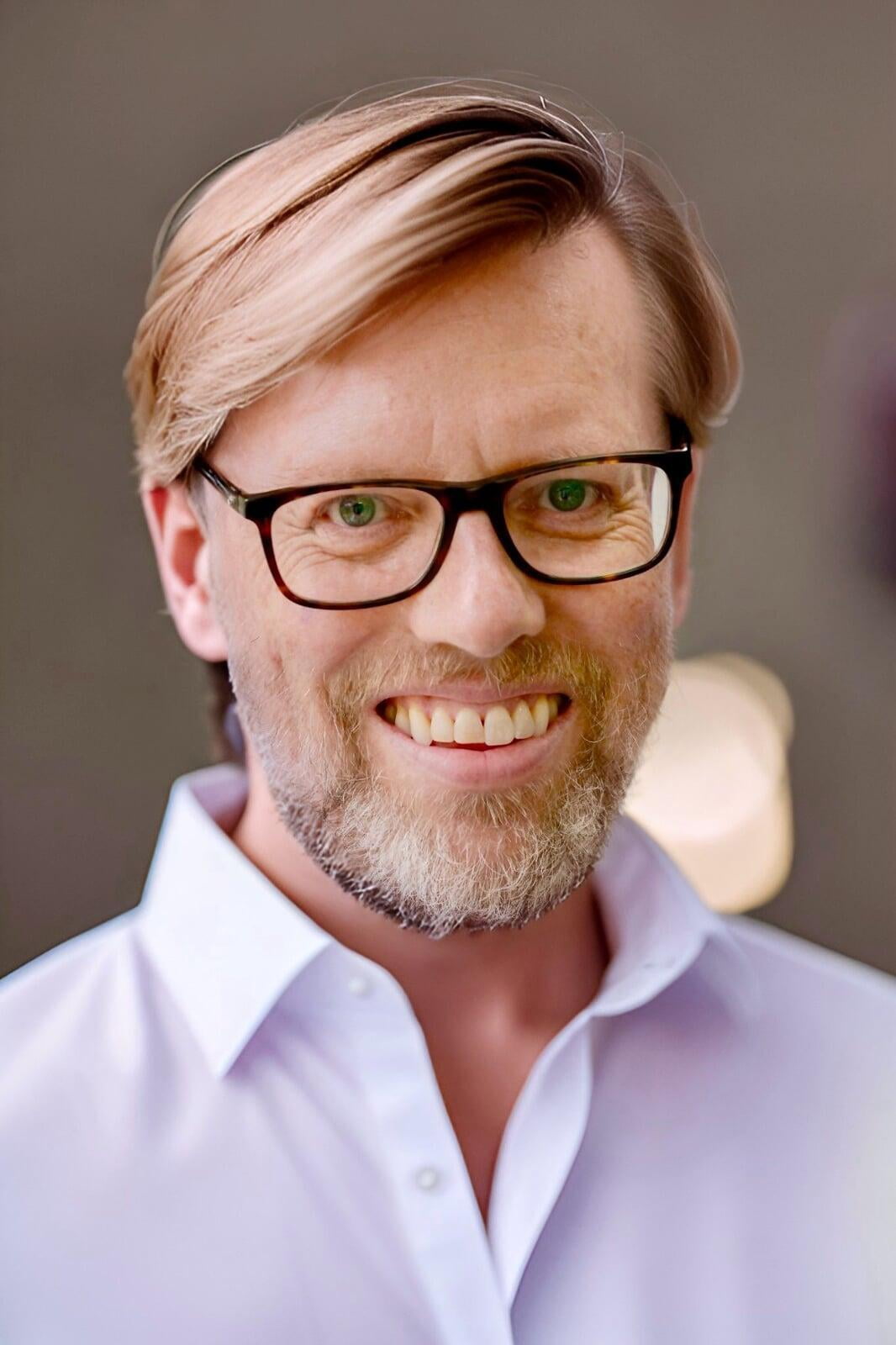
Greg Livingstone
Greg Livingstone
Fluitec